Introduction: The Hidden Strength Behind Every Delivery
Have you ever wondered how a delicate porcelain vase or a bulky electronic device reaches your doorstep in perfect condition after a long, bumpy journey? The unsung hero of this achievement is the corrugated box, a silent guardian in the world of logistics. These seemingly humble containers form the sturdy backbone of shipping and storage, safeguarding everything from fragile keepsakes to robust industrial equipment.
For businesses, they represent more than mere packaging—they embody a commitment to delivering products as flawless as the day they left the warehouse. So, what exactly powers the remarkable resilience of corrugated boxes, and why should they matter to you? Let’s delve into their ingenious structure, diverse options, and transformative advantages, particularly if you’re a packaging buyer or manager seeking reliable and cost-effective solutions.

Why Corrugated Boxes Are a Game-Changer for Your Business
Shipping products without proper protection is akin to stepping into a tempest without a shield—you’re destined to face disaster. Faulty packaging leads to damaged goods, exorbitant shipping expenses, and inefficient solutions that waste valuable space, posing persistent challenges for businesses.
The root cause often lies in substandard materials that simply can’t endure. However, corrugated cardboard emerges as a powerhouse, surpassing ordinary cardboard with its remarkable strength and ability to absorb impacts. Whether you’re transporting delicate cosmetics or heavy-duty equipment, these boxes act as a steadfast guardian, cushioning contents against harsh conditions.
Moreover, by adopting sustainable packaging solutions through corrugated boxes, which are crafted from recycled fibres, you not only bolster your brand’s eco-friendly reputation in a sustainability-driven market but also contribute to a greener future.
Breaking Down the Basics: What Is a Corrugated Box?
Picture a small stronghold crafted from humble paper—that’s the essence of a corrugated box. Formed from corrugated fibreboard, it’s an ingenious assembly of kraft paper layers. Envision it as a sturdy sandwich: two smooth sheets, known as liners, encase a rippled core called fluting. This undulating structure isn’t merely decorative; it acts as a formidable buffer, absorbing shocks and resisting pressure from all angles. Moreover, the air pocketed within these flutes serves as natural insulation, shielding the contents from erratic temperature shifts, much like an invisible thermal blanket.
In stark contrast to ordinary cardboard, which falters under strain, corrugated fibreboard excels in the demanding arena of shipping. Bound by a robust, often starch-based adhesive through a precise process involving a machine called a corrugator, these layers merge into an unyielding structure, primed to withstand the rigours of transit.
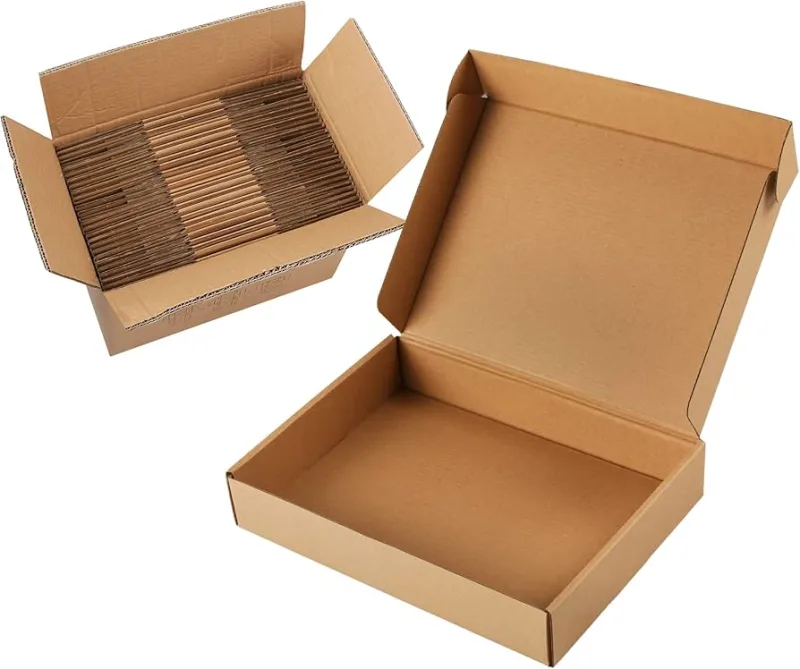
Exploring the Variety: Types of Corrugated Boxes
Corrugated boxes are far from a universal solution—they come in an array of styles tailored to diverse requirements. Let’s dive into a concise overview to help you pair the ideal box with your product’s needs:
- Singleface: A minimalist pairing of a single liner and a corrugated layer. It’s as light as a breeze, commonly rolled for cushioning delicate items or as internal padding, though it lacks the sturdiness for standalone shipping tasks.
- Single Wall: The reliable backbone of packaging, featuring a lone corrugated layer nestled between two liners. This is the go-to cardboard choice for routine shipping demands.
- Double Wall: A sturdier contender, built with two corrugated layers and three liners, making it a robust shield for heavier industrial goods that crave added protection.
- Triple Wall: The unrivalled champion, constructed with three corrugated layers and four liners. Its formidable strength allows it to rival wooden crates, often tasked with transporting hefty loads like chemical drums.
Selecting the right type is akin to picking the perfect armour for battle—don’t equip a paper shield for a heavyweight clash! Ultimately, your decision rests on factors like the product’s weight, fragility, and shipping conditions, ensuring a seamless journey from start to finish.
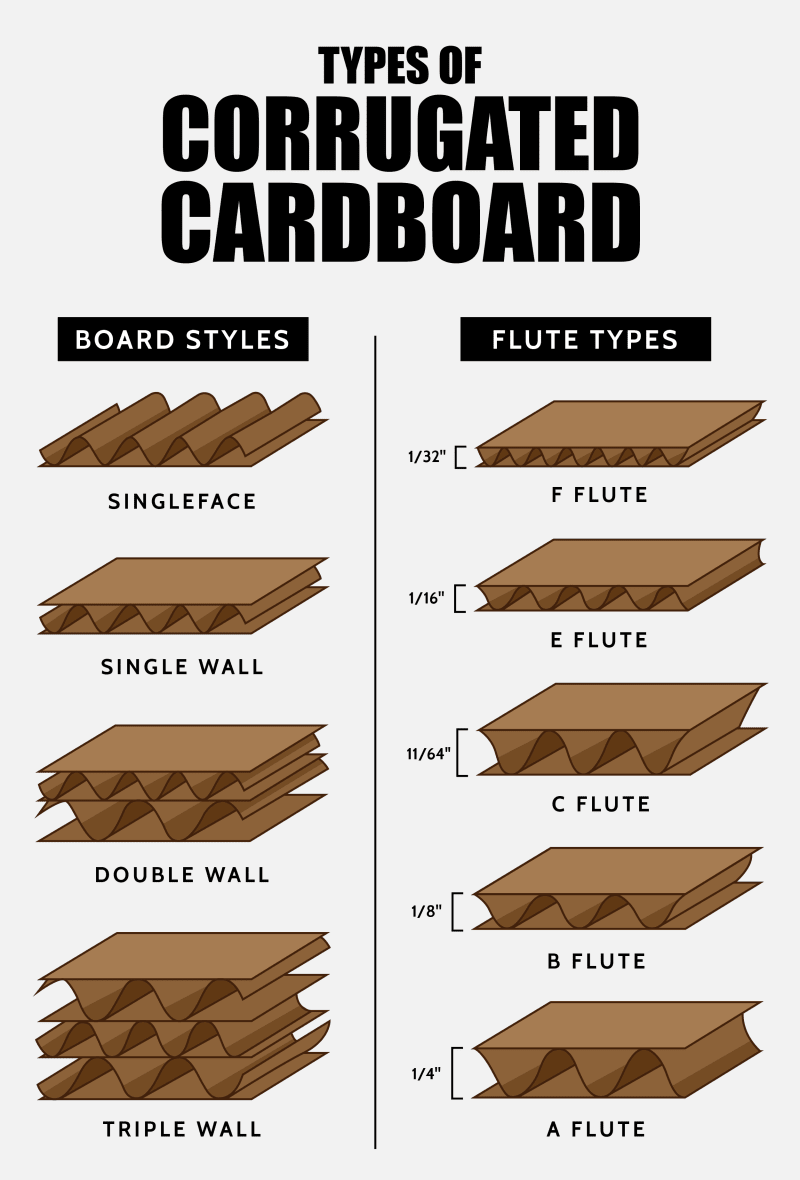
The Hidden Edge: How Flute Sizes Shape Performance
The true brilliance of corrugated boxes unfolds through their flute sizes and profiles—the undulating inner layers that determine both durability and purpose. Each variant plays a unique part in the packaging puzzle:
- A Flute (1/4” thick): As the thickest of the bunch, it provides unparalleled cushioning and stacking strength. It acts as a guardian for fragile goods, offering a protective shield against bumps and knocks.
- B Flute (1/8” thick): Though narrower, it stands resilient against crushing pressures while boasting a flawless surface for sharp, vivid printing. Often, it’s the choice for inner components like dividers or trays.
- C Flute (5/32” thick): This all-rounder strikes a balance with impressive crush resistance and dominates box manufacturing processes, forming the backbone of about 80% of shipments, from food to furniture.
- E Flute (1/16” thick): Sleek and resourceful, it still holds firm under strain. It’s frequently tapped for elegant packaging solutions, such as pizza boxes or cosmetic containers.
- F Flute (1/32” thick): A microflute masterpiece, its ultra-dense structure ensures exceptional crush resistance. You’ll find it safeguarding fast-food packs or delicate jewelry cases.
Imagine flutes as the suspension system of a vehicle—thicker profiles absorb the harshest shocks, whereas slimmer ones offer agility and finesse. Therefore, selecting the ideal flute can indeed be the critical factor between a seamless delivery and a costly mishap. Furthermore, understanding their distinct strengths ensures smarter choices for every payload.
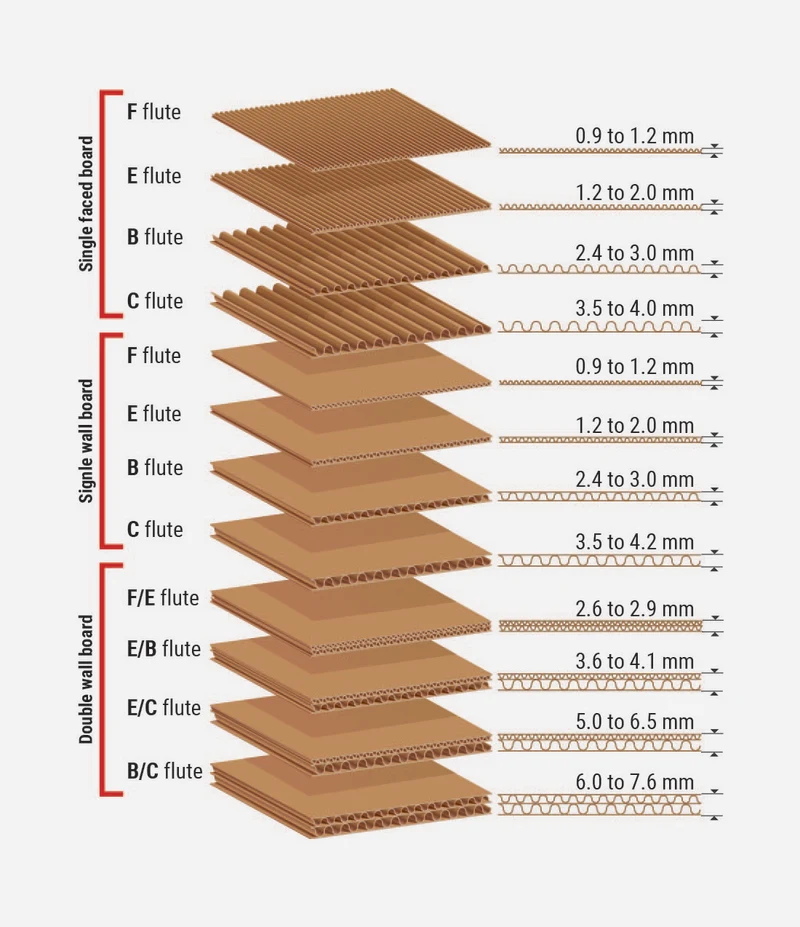
Behind the Scenes: Crafting a Corrugated Box
The box manufacturing process unfolds like a captivating symphony of precision and ingenuity. It begins with enormous rolls of kraft paper—one destined for robust liners, the other for the rippled fluting. These are guided into a formidable corrugator machine, where steam and colossal rollers mould the fluting paper into uniform waves. A touch of starch-based adhesive binds these waves to the liners, creating a sturdy single wall board, or additional layers for double and triple wall variations.
Subsequently, the board is expertly cut into sheets or tailored widths, before being dispatched to converting machines for the final refinements—think printing, slotting, folding, and gluing into their ultimate form. Often, to maximise efficiency, boxes are delivered as flat “blanks” to conserve space, eagerly awaiting assembly at the packing line. It’s akin to witnessing an artisan at work; indeed, every precise cut and calculated fold is intentional, resulting in a impeccable custom box design.
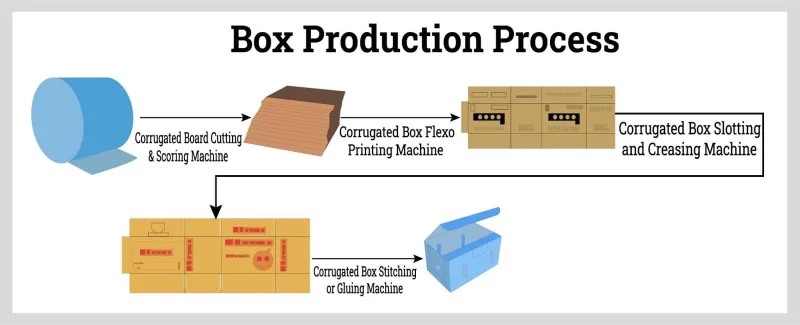
Green and Mighty: Why Corrugated Boxes Lead in Sustainability
Here’s a delightful fact to consider: corrugated boxes are champions among recyclable packaging materials. Crafted from kraft paper derived from renewable wood pulp, they are fully biodegradable and often made from up to 100% recycled fibers. After serving their purpose, they seamlessly re-enter the recycling cycle, with fibers reusable up to 25 times, thus minimising waste and conserving precious resources. This perfectly mirrors the sustainable packaging solutions that modern, eco-conscious businesses strive to embrace.
Moreover, their feather-light design significantly reduces fuel consumption during transportation—less weight translates to fewer emissions. This is a triumph for the environment. At innovative hubs like C MIC Packaging, sustainability is not just a trend but a core commitment, marrying top-notch quality with planet-friendly ethos. Each box dispatched becomes a subtle yet powerful step towards a more verdant future.
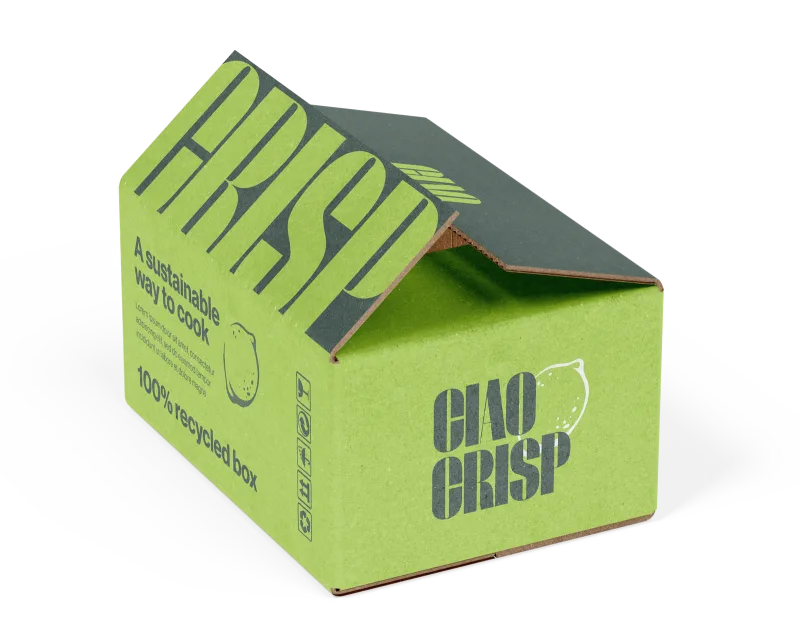
Stress-Tested: Ensuring Your Corrugated Box Won’t Buckle
Curious whether your boxes can endure the rigours of transit? Rest assured, industry standards like the Mullen Burst Test assess a box’s resilience by determining the exact pressure—in pounds per square inch or kilopascals—it can endure before giving way. This test is vital for shipments with dynamic loads such as fruit or beads, where single-wall boxes typically achieve ratings between 23 and 32, with higher scores reflecting greater toughness.
Moreover, the Edge Crush Test (ECT) evaluates the stacking prowess of these warehouse champions by measuring the vertical compression strength of the board’s edges. These rigorous assessments elevate your boxes from simple cardboard to fortified bastions. With reliable partners like C MIC Packaging, quality control becomes a steadfast promise rather than a roll of the dice, ensuring that boxes not only meet but exceed these benchmarks, delivering unshakable confidence.
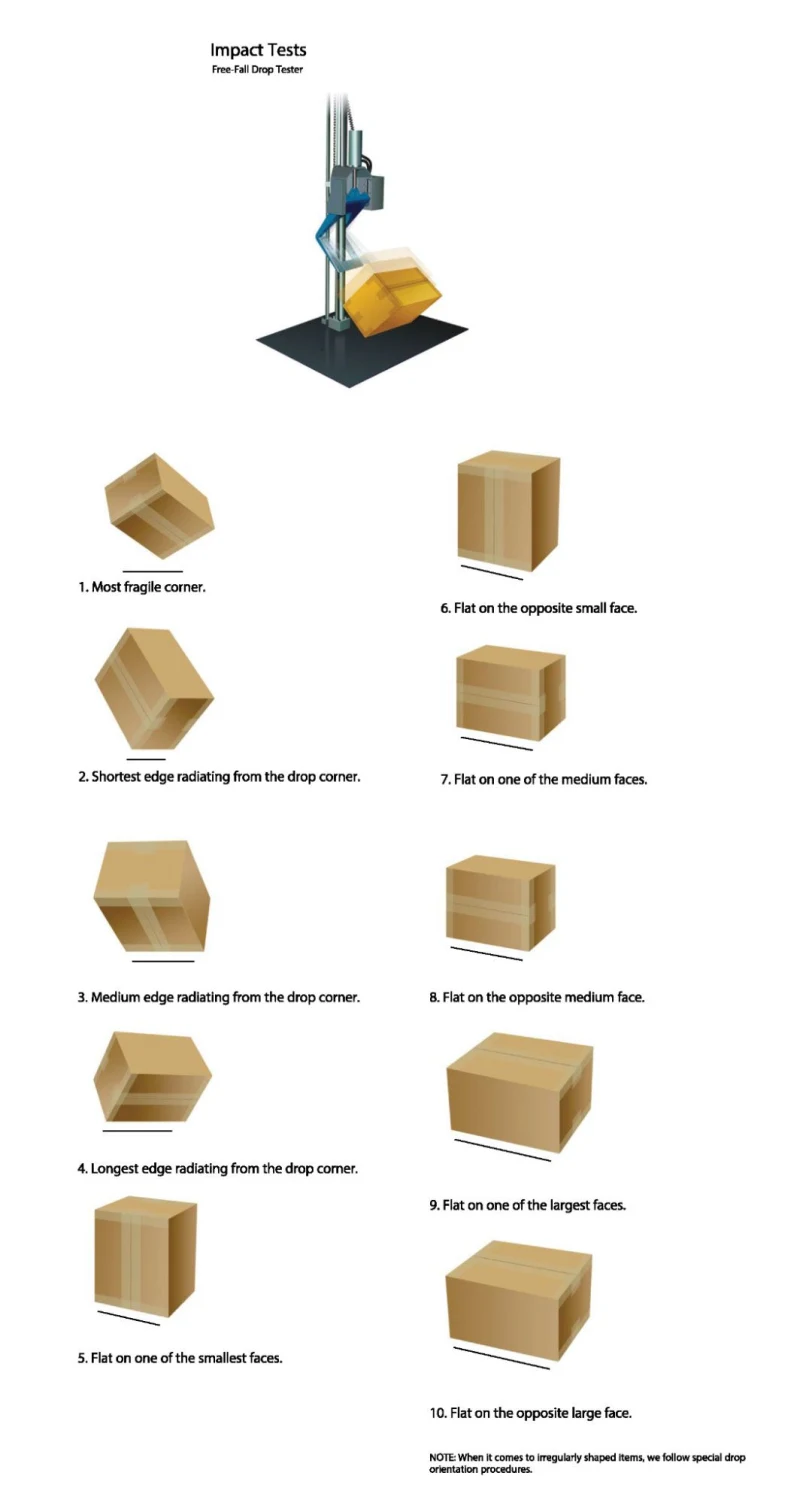
Tailored to You: Customising Corrugated Boxes
Absolutely, without a doubt! Custom box design is where corrugated packaging truly showcases its strength and versatility. Whether you require an unusual size for a unique product or eye-catching graphics to captivate your audience, the options are virtually limitless. Printing techniques vary from rapid flexographic methods for straightforward designs to advanced digital CMYK printing with UV cure for vivid, high-quality logos. Box styles, such as regular slotted containers (RSC) or wraparound designs, effortlessly integrate into both automated and manual packing systems.
Moreover, for added protection, you can incorporate custom inserts, dividers, or pads to safeguard delicate items. Handling hefty goods? Double or triple wall constructions provide the robust support you need. Collaborators like C MIC Packaging excel in delivering tailor-made solutions, ensuring your packaging perfectly aligns with your product’s distinct requirements. It’s akin to crafting a bespoke masterpiece—every element mirrors your creative vision.
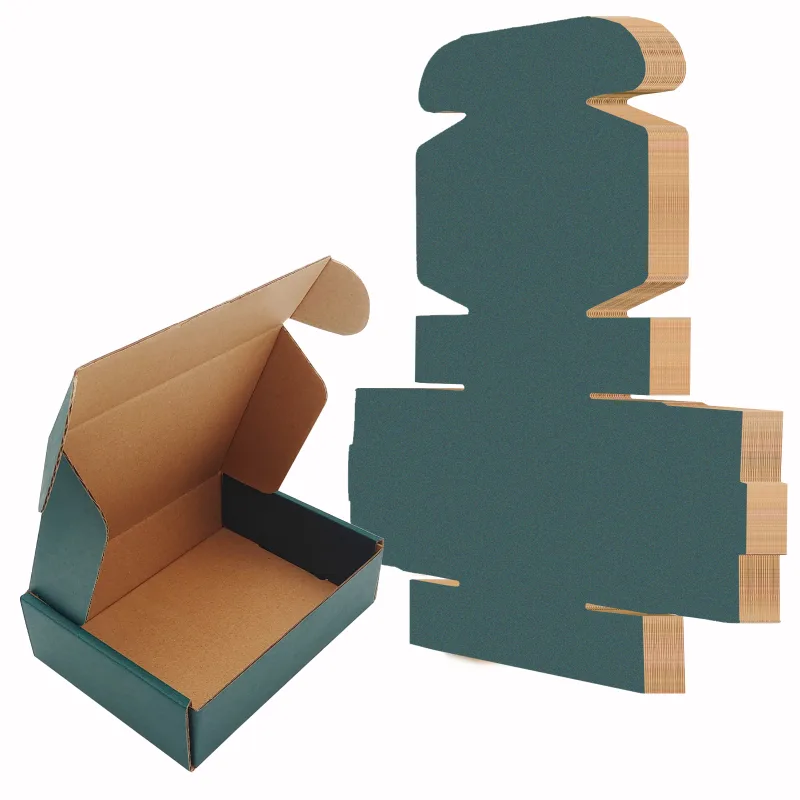
Weighing It Up: Benefits and Drawbacks of Corrugated Boxes
Let’s delve into the details. On the positive side, corrugated boxes boast remarkable strength and durability, safeguarding products from impacts and damage with their unique fluted structure acting as a protective shield. Their adaptability in size, flute variations, and design ensures they embrace almost any product with tailor-made precision. Moreover, as recyclable packaging materials, they effortlessly capture the hearts of environmentally aware consumers.
However, challenges do arise. They lack innate resistance to water, meaning moisture can weaken their integrity unless fortified with wax or other protective layers. Overloading them invites disaster, so it’s crucial to pair the right box with the appropriate load. While custom designs offer fantastic potential, they can delay schedules if not orchestrated in advance. Ultimately, it’s about finding harmony, much like fine-tuning a recipe for the perfect flavour.
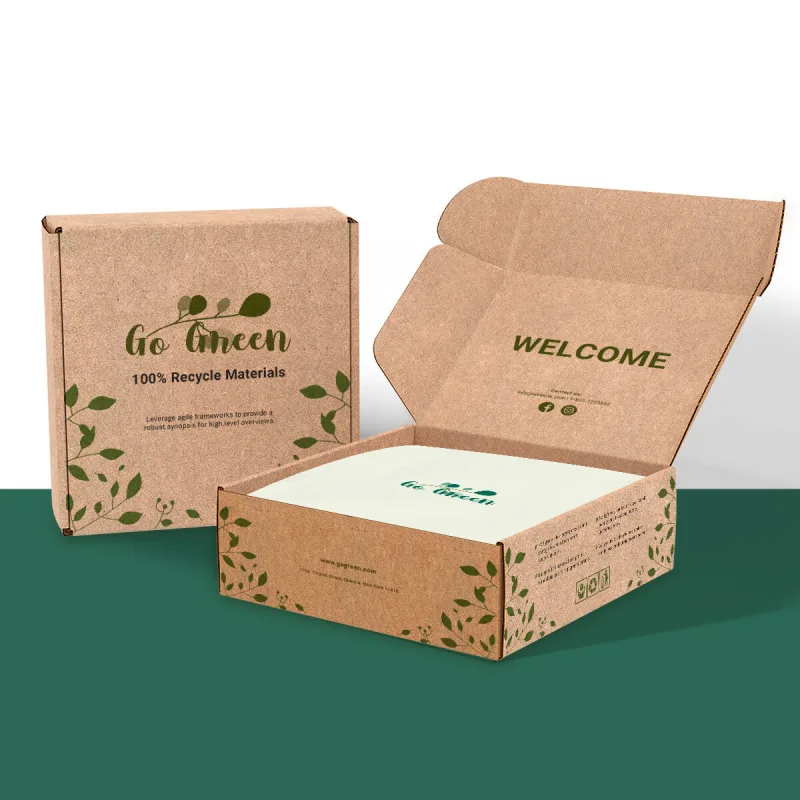
Wrapping Up: Ready to Transform Your Packaging?
Corrugated boxes aren’t mere containers; they’re your product’s shield against the chaos of shipping and handling. Armed with insights on types of corrugated boxes and the right flute sizes and profiles, you’re set to make savvy choices. Their unmatched strength and durability, coupled with eco-friendly appeal, make them a no-brainer for any business.
Ready to see how these powerhouses can solve your unique challenges? Connect with a trusted name like C MIC Packaging for personalized guidance and solutions. Let’s guarantee your products arrive safe, secure, and sustainably packaged—because every delivery tells a story worth sharing!